El uso de la tecnología de revestimiento de plasma para fortalecer la superficie de las brocas PDC es un medio eficaz para mejorar su resistencia al desgaste, al impacto y a la corrosión.
1. Etapa de preparación
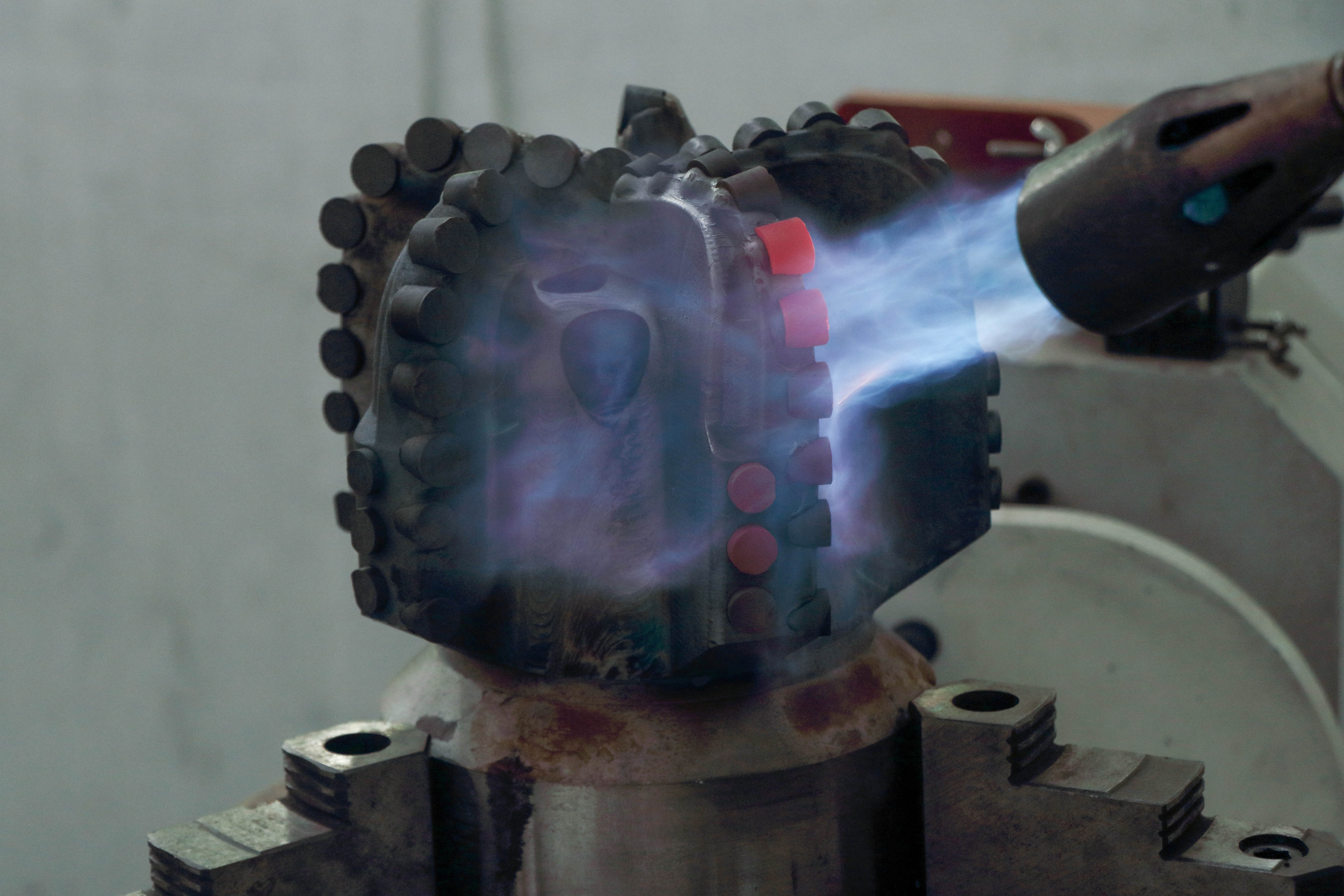
(1) Determinar el material del revestimiento
- Materiales de revestimiento más utilizados:
- Aleación a base de cobalto: alta resistencia al desgaste y a la corrosión.
- Aleación a base de níquel: resistente a la oxidación a alta temperatura y a la corrosión química.
- Aleaciones a base de hierro: rentables y adecuadas para requisitos de resistencia al desgaste medio.
- Aleaciones reforzadas con partículas cerámicas: p. ej. WC (carburo de tungsteno), TiC (carburo de titanio), etc. para requisitos de resistencia al desgaste muy elevados.
(2) Determinación del área de revestimiento
- El revestimiento por fusión de las brocas de PDC suele tener como objetivo:
- Parte del flanco: para mejorar la resistencia al desgaste y reducir la fricción y la pérdida de corte.
- La superficie de la carcasa: para mejorar la resistencia general a la corrosión y al impacto.
(3) Pretratamiento de superficies
- Limpiar la zona del revestimiento para eliminar aceite, óxidos, recubrimientos e impurezas.
- Tratamiento mecánico de rectificado o arenado para aumentar la rugosidad de la superficie y mejorar la unión de la capa de revestimiento fusionada con el sustrato.
2. Implementación del proceso de revestimiento
(1) Configuración del equipo de revestimiento de plasma
- Composición del equipo:
pistola de soldadura de plasma, alimentador de polvo, máquina de soldadura de plasma automatizada, etc..
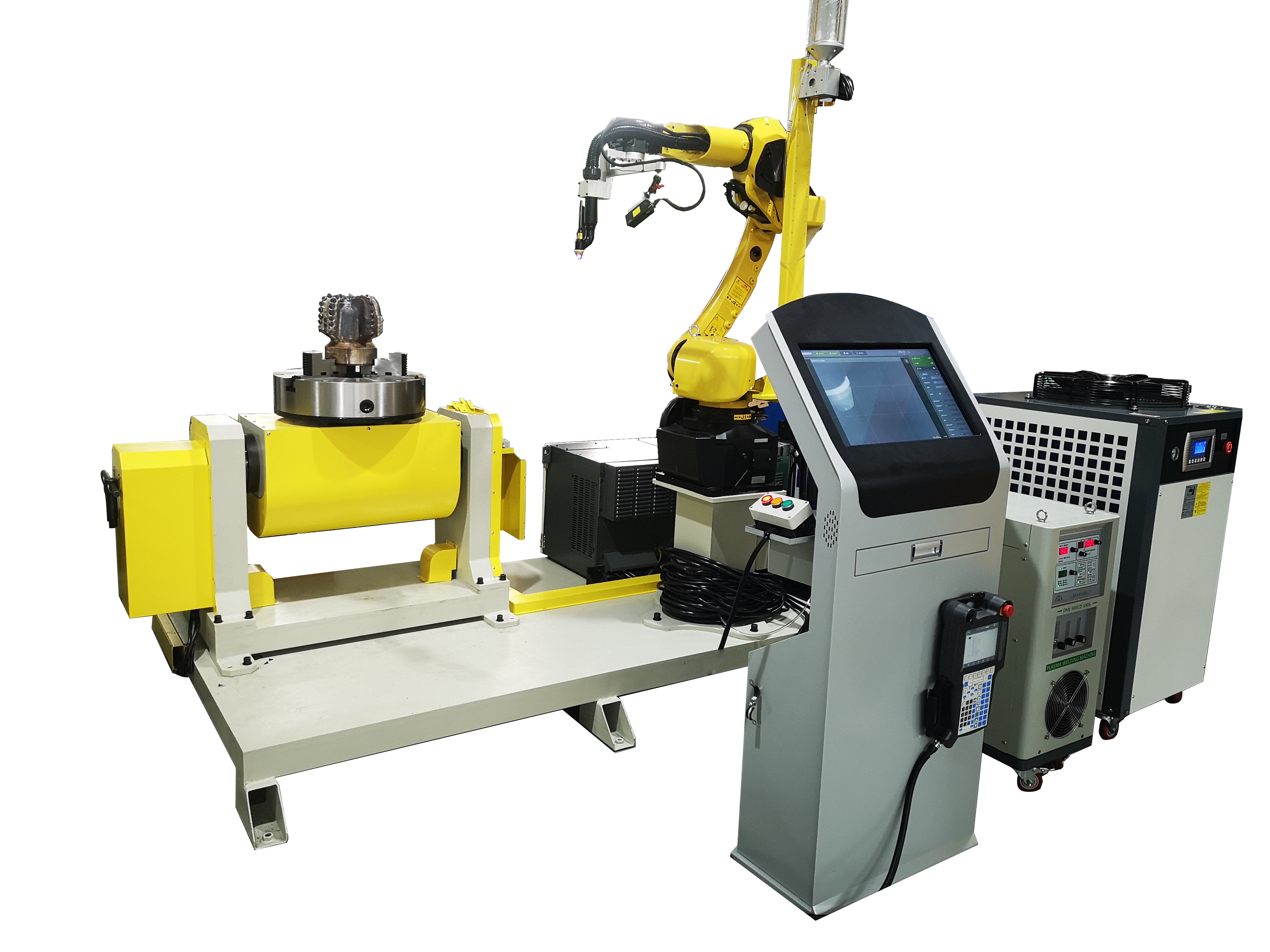
- Establecer los parámetros clave:
- Corriente y voltaje de arco: seleccionar según el material a recubrir, generalmente en el rango de 100-300A.
- Entrada de calor: ajuste para controlar la deformación del sustrato y la tasa de dilución.
- Velocidad de alimentación de polvo: generalmente en el rango de 10 ~ 50 g/min para garantizar la uniformidad de la capa de revestimiento.
(2) Ejecución del revestimiento
- El proceso de revestimiento:
1. Se inicia el arco de plasma y se forma un baño de fusión de alta temperatura.
2. A través del sistema de alimentación de polvo, el material en polvo se rocía en el baño de fusión y se une metalúrgicamente con el sustrato.
3. de acuerdo con la forma de la broca, a lo largo del camino establecido para un revestimiento uniforme, para garantizar que no haya fugas de revestimiento o sobrefusión.
- Controlar la influencia térmica: evitar el sobrecalentamiento o la deformación del sustrato de la broca PDC ajustando los parámetros del arco de plasma y el método de enfriamiento.
(3) Tratamiento de enfriamiento
- Enfriamiento natural o adopción de un método de enfriamiento de velocidad controlada para evitar grietas causadas por estrés térmico.
3. Etapa de postratamiento
(1) Inspección de la calidad del revestimiento
- Inspección de apariencia: Observe si la capa de revestimiento es uniforme, libre de grietas y agujeros de aire.
- Prueba de rendimiento: medir la dureza, el espesor (generalmente entre 0,5 y 3 mm), la fuerza de unión y otros indicadores.
- Pruebas no destructivas: utilice pruebas ultrasónicas o de rayos X para solucionar defectos internos.
(2) Acabado
- Si la superficie es rugosa después del revestimiento por fusión, se requiere un tratamiento de torneado o rectificado para cumplir con los requisitos de tamaño y forma de las brocas PDC.
(3) Optimización del rendimiento
- Tratamiento térmico: templar o revenir la capa de revestimiento fusionada si es necesario para optimizar aún más sus propiedades organizativas.
4. Precauciones
1. Evite daños por sobrecalentamiento
- Durante el revestimiento de plasma, la entrada de calor debe controlarse estrictamente para evitar daños térmicos al inserto de PDC y al sustrato.
2. Coincidencia de materiales
- El material de revestimiento debe coincidir con el material del sustrato de la broca PDC para garantizar la resistencia de la unión y la consistencia del rendimiento.
3. Control ambiental
- En la medida de lo posible en ambiente de baja humedad o con gas protector para evitar oxidaciones que afecten a la calidad del revestimiento.
Este proceso se puede utilizar para mejorar el rendimiento de brocas PDC nuevas así como para reparar brocas desgastadas.
Hora de publicación: 09-ene-2025