Es gibt viele verschiedene Schweißverfahren, jedes mit seinen eigenen Prinzipien, Vor- und Nachteilen sowie Anwendungsbereichen. Im Folgenden finden Sie eine detaillierte Beschreibung gängiger Schweißverfahren, einschließlich Prinzipien, Eigenschaften, Vor- und Nachteilen, Anwendungsbereichen und einer vergleichenden Analyse mit anderen Schweißverfahren.
1. Klassifizierung der Schweißverfahren
Schweißverfahren lassen sich grob in folgende Kategorien einteilen:
•Schmelzschweißen (z. B. Lichtbogenschweißen, Laserschweißen usw.): Verschmelzen von Metallen durch Erhitzen bis zum Schmelzzustand.
•Pressschweißen (z. B. Reibschweißen, Diffusionsschweißen etc.): Verbinden von Metallen durch Druckeinwirkung, ohne dass sie aufschmelzen.
•Löten (z. B. Weichlöten, Hartlöten): Verbinden von Werkstücken mit niedrigschmelzenden Zusatzwerkstoffen.
2. Gängige Schweißverfahren erklärt
2.1 SMAW – Metallschutzgasschweißen
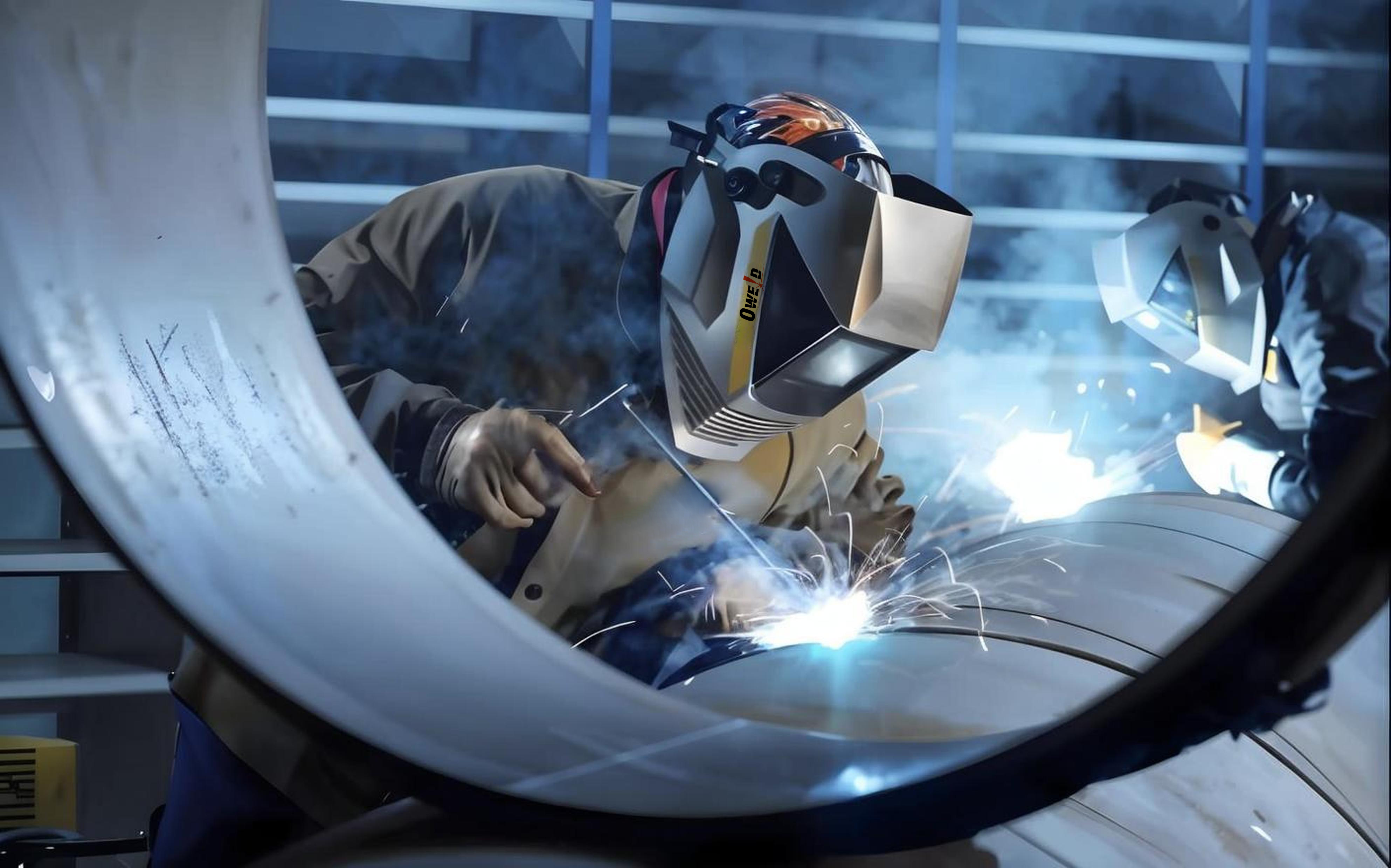
Prinzip: Beim manuellen Lichtbogenschweißen wird ein Lichtbogen zwischen Elektrode und Grundmaterial erzeugt, um hohe Temperaturen (ca. 4000 °C) zu erzeugen. Dadurch schmelzen Elektrode und Grundmaterial und bilden eine Schweißnaht. Die Elektrodenbeschichtung erzeugt während des Schweißvorgangs Schutzgas, um eine Oxidation der Schweißnaht zu verhindern.
Merkmale:
Schweißen mit Schweißdraht (Kern + Flussmittelumhüllung).
Geeignet zum Schweißen in verschiedenen Positionen, wie zum Beispiel Stehschweißen und Gegenschweißen.
Kann im Freien mit geringen Umweltanforderungen betrieben werden.
Vorteile:
Einfache Ausstattung, flexible Bedienung, geeignet für Feld- oder Wartungsarbeiten.
Kann verschiedene Metalle schweißen, wie Kohlenstoffstahl, Edelstahl, Gusseisen usw.
Geeignet zum Schweißen komplex geformter Werkstücke.
Nachteile:
Geringe Schweißeffizienz, Schweißdraht muss häufig ausgetauscht werden.
Die Qualität der Schweißnaht wird stark von der Technik des Schweißers beeinflusst und es können leicht Schweißfehler (wie Porosität und Schlacke) entstehen.
Beim Schweißen entstehen mehr Rauch und Staub, was die Umwelt stärker belastet.
Anwendungen:
Geeignet für Bau, Instandhaltung, Brückenbau, Pipelinebau, Schiffbau und andere Branchen.
Geeignet für kleine Projekte und Feldeinsätze.
2.2 GMAW - Metall-Schutzgasschweißen
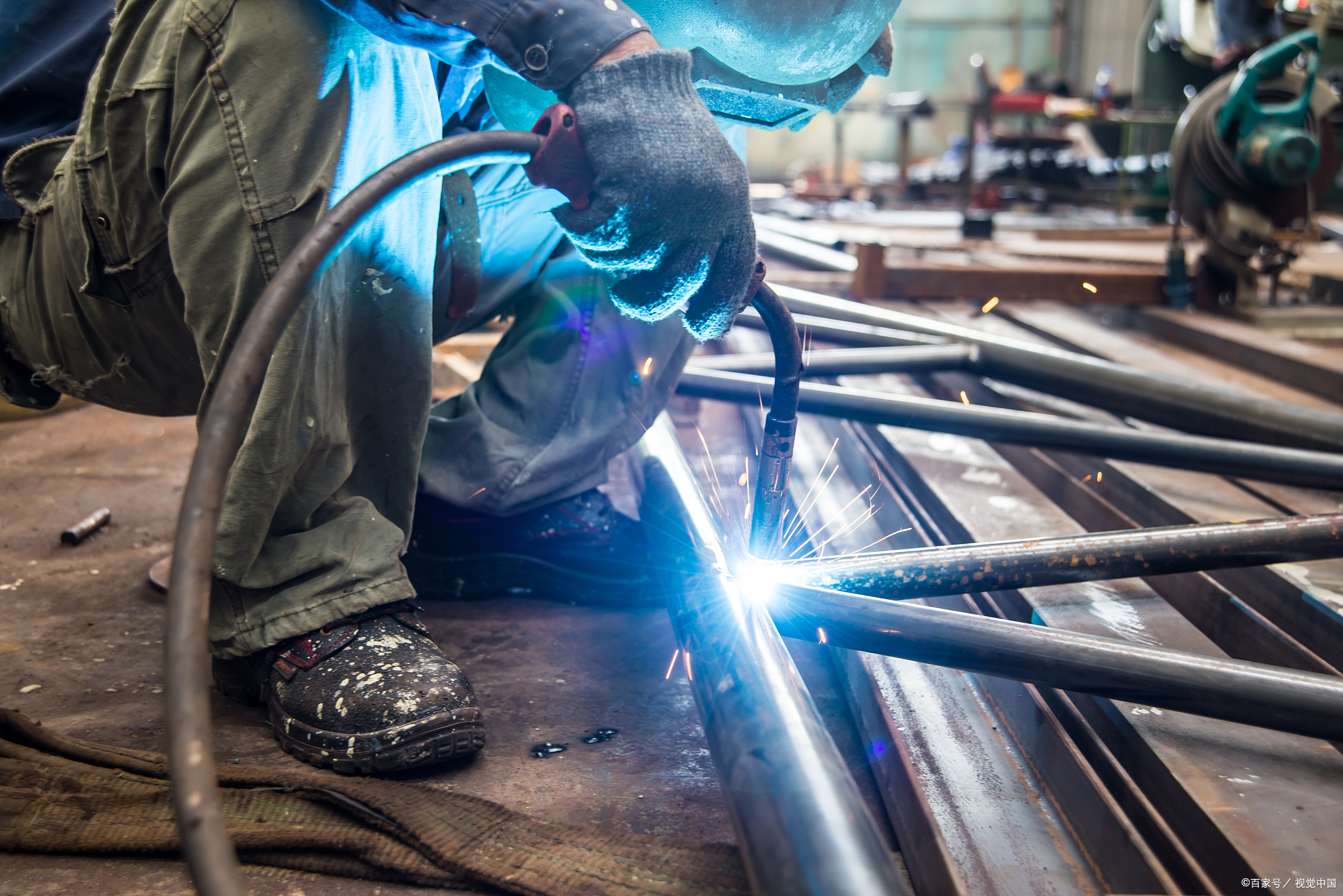
Prinzip:Beim Schutzgasschweißen wird ein kontinuierlich zugeführter Draht als Elektrode verwendet, der in einer Schutzgasumgebung (z. B. Argon oder Kohlendioxid) einen Lichtbogen erzeugt, der den Draht und das Grundmaterial zum Schmelzen bringt und so eine Schweißnaht bildet.
Einstufung:
MIG-Schweißen (Metal Inert Gas): Verwendung von Inertgas (z. B. Argon), geeignet für Aluminiumlegierungen, Edelstahl und andere Materialien.
MAG-Schweißen (Metal Active Gas): Verwendung von Aktivgas (Kohlendioxid oder Mischgas), geeignet zum Schweißen von Weichstahl und Baustahl.
Merkmale:
Einführung einer automatischen Drahtzufuhr zur Verbesserung der Schweißeffizienz.
Glatte Schweißoberfläche und stabile Schweißqualität.
Empfindlich gegenüber Umwelteinflüssen (Wind, Feuchtigkeit), nicht für den Außenbau geeignet.
Vorteile:
Schnelle Schweißgeschwindigkeit, geeignet für die Massenproduktion.
Kann zum Schweißen dünner Platten und geringer Verformung verwendet werden.
Automatisiertes Schweißen, beispielsweise Roboterschweißen, ist leicht zu realisieren.
Nachteile:
Höhere Gerätekosten, Gasversorgungssystem erforderlich.
Kann nicht in einer Umgebung mit starkem Wind verwendet werden, da sonst das Schutzgas weggeblasen wird und die Qualität der Schweißnaht beeinträchtigt wird.
Geeignet für saubere Metalloberflächen, nicht geeignet für stark rostende oder ölverschmutzte Werkstücke.
Anwendungen:
Automobilbau, Schiffe, Brücken, Haushaltsgeräteindustrie usw.
Geeignet für eine hocheffiziente und qualitativ hochwertige industrielle Produktion.
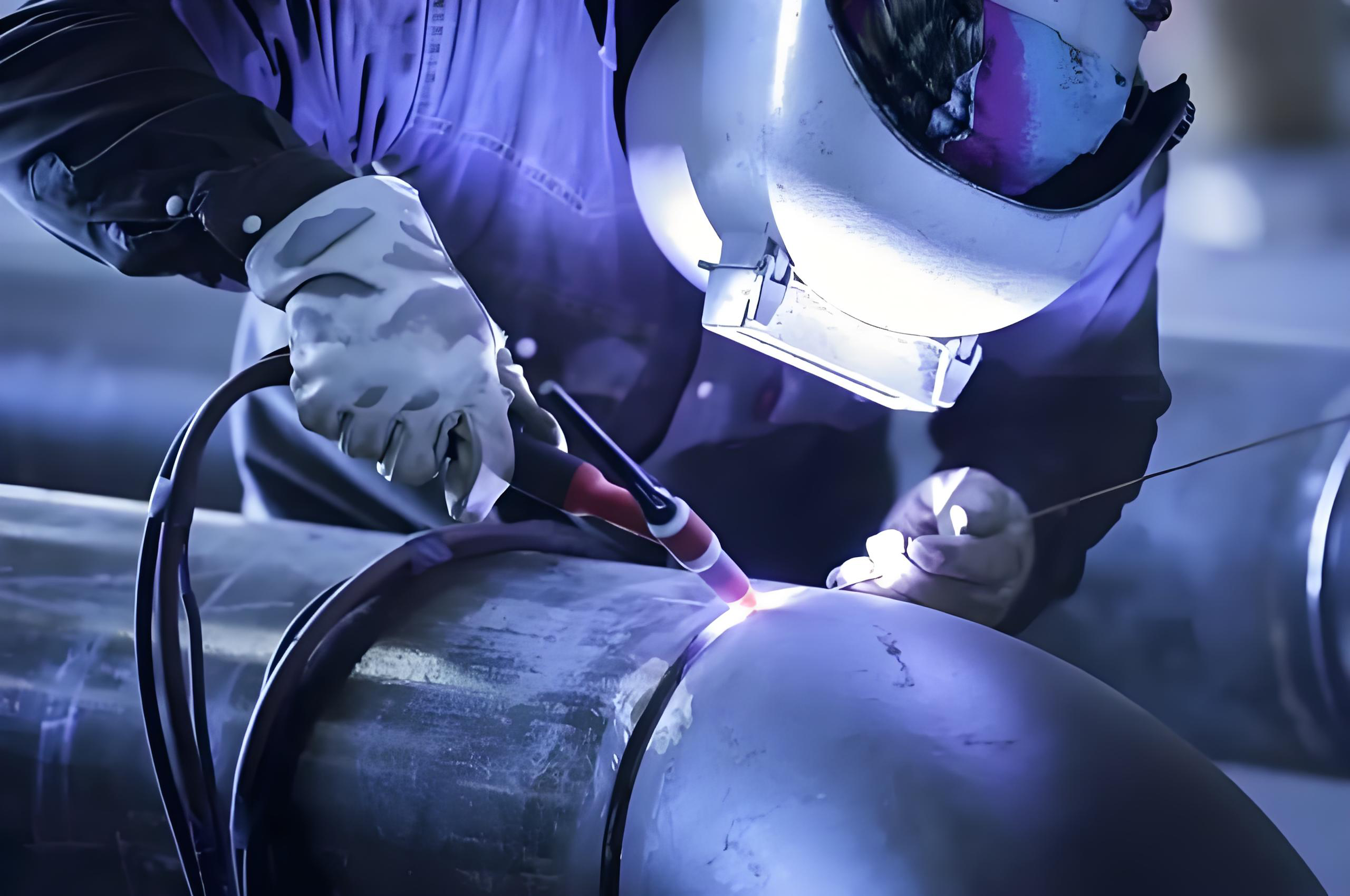
Prinzip: Beim WIG-Schweißen wird mit einer nicht schmelzenden Wolframelektrode ein Lichtbogen erzeugt, der unter Argonschutz das Grundmetall und das Füllmetall schmilzt und so eine Schweißnaht bildet.
Merkmale:
Hohe Schweißqualität, glatte und schöne Schweißnaht.
Geeignet für hochpräzises Schweißen, beispielsweise in der Luft- und Raumfahrt und bei medizinischen Geräten.
Geeignet zum Schweißen dünner Platten und Nichteisenmetalle (Aluminium, Kupfer, Titan).
Vorteile:
Schweißnaht ohne Spritzer, hohe Qualität, geeignet für Präzisionsschweißungen.
Geeignet zum Schweißen unterschiedlicher Metalle.
Schutzgas (Argon) verhindert wirksam die Oxidation der Schweißnaht.
Nachteile:
Langsame Schweißgeschwindigkeit, geringe Effizienz.
Teure Ausrüstung, hohe Qualifikationsanforderungen an Schweißer.
Wird durch Wind beeinflusst, nicht zum Schweißen im Freien geeignet.
Anwendungen:
Luft- und Raumfahrt, Elektronik, Medizin und Präzisionsfertigung.
Schweißen von Edelstahlrohren und Strukturteilen aus Aluminiumlegierungen
2.4 Unterpulverschweißen
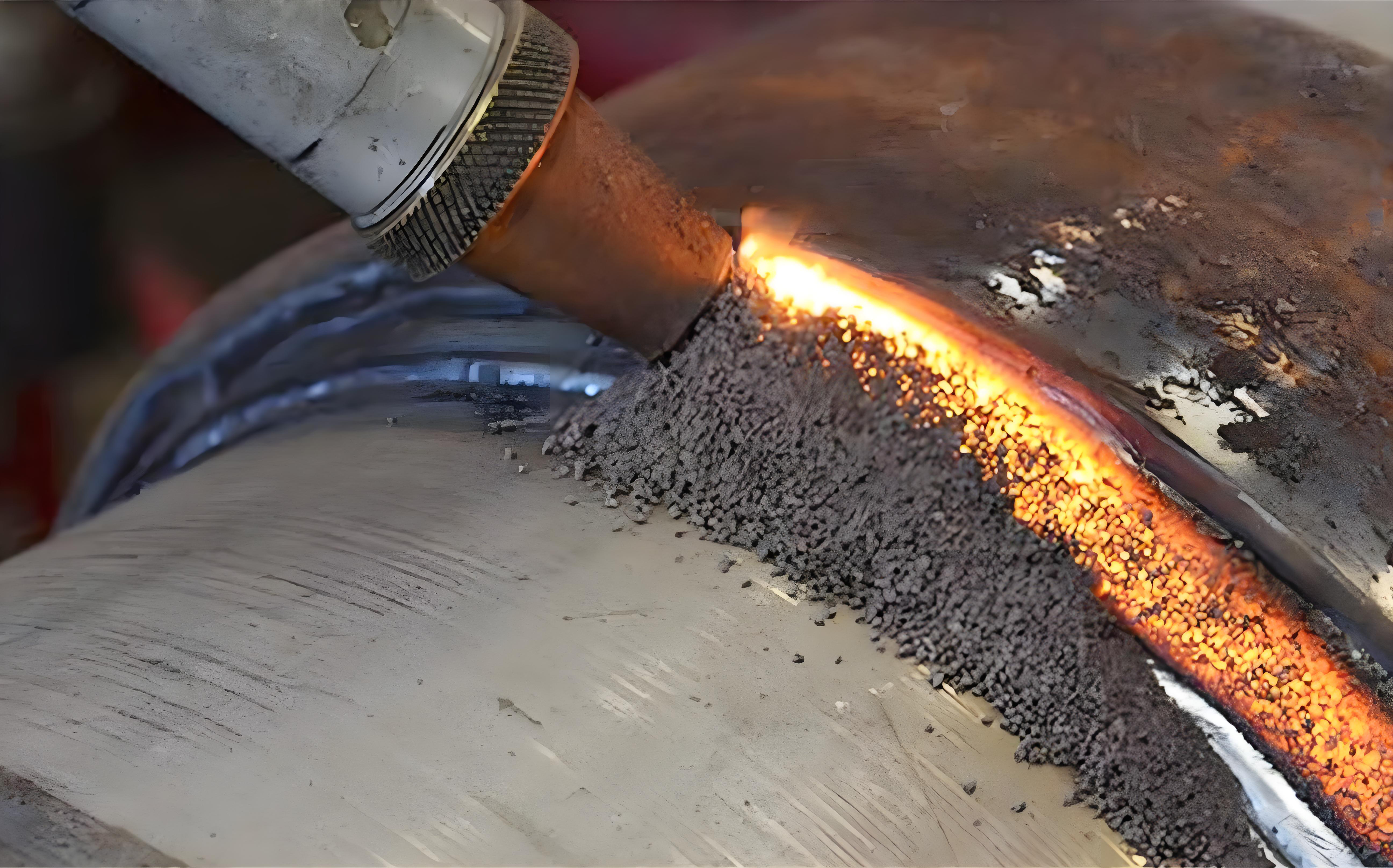
Prinzip:Beim Unterpulverschweißen wird der Lichtbogen mit einem Flussmittel bedeckt, das bei hohen Temperaturen schmilzt und eine Schutzschicht bildet, die die Schweißnaht luftfrei hält.
Merkmale:
Geeignet zum Schweißen dicker Platten, beispielsweise im Brücken- und Kesselbau.
Kann nur für horizontales Schweißen verwendet werden, nicht für vertikales Schweißen, Höhenschweißen und andere Positionen.
Vorteile:
Schnelle Schweißgeschwindigkeit, hohe Effizienz, geeignet für die Massenproduktion.
Hohe Schweißqualität, Flussmittel verhindert Schweißfehler (Porosität, Risse).
Keine Lichtbogenbelastung, weniger Schweißrauch, verbesserte Arbeitsumgebung.
Nachteile:
Kann nur zum Schweißen gerader Linien verwendet werden, gilt nicht für das Schweißen komplexer Formen.
Größere Geräte, nicht zum Schweißen kleiner Teile geeignet.
Anwendungen:
Schweißen von dicken Platten, Rohren, Brücken und Druckbehältern.
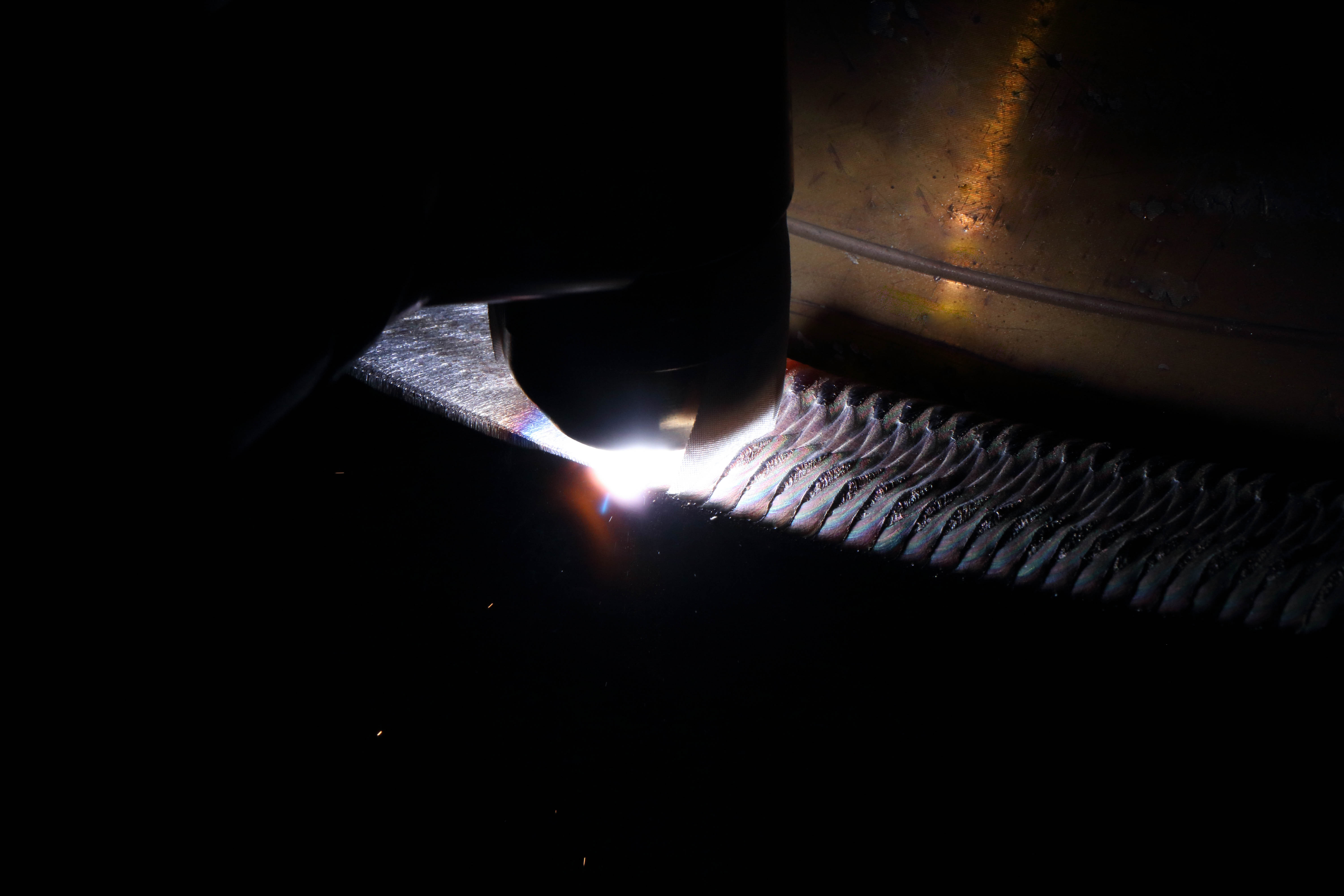
Prinzip:Schweißen mit einem Hochtemperatur-Plasmalichtbogen zum Schmelzen von Metall.
Vorteile:
Konzentrierte Energie, geringer Schweißverzug.
Geeignet für Präzisionsschweißungen, beispielsweise von dünnwandigen Materialien.
Nachteile:
Hohe Kosten für die Ausrüstung, komplexe Wartung.
Hohe Anforderungen an die Bedienkompetenz.
Anwendungen:Luft- und Raumfahrt, medizinische Geräte, Elektronikindustrie.
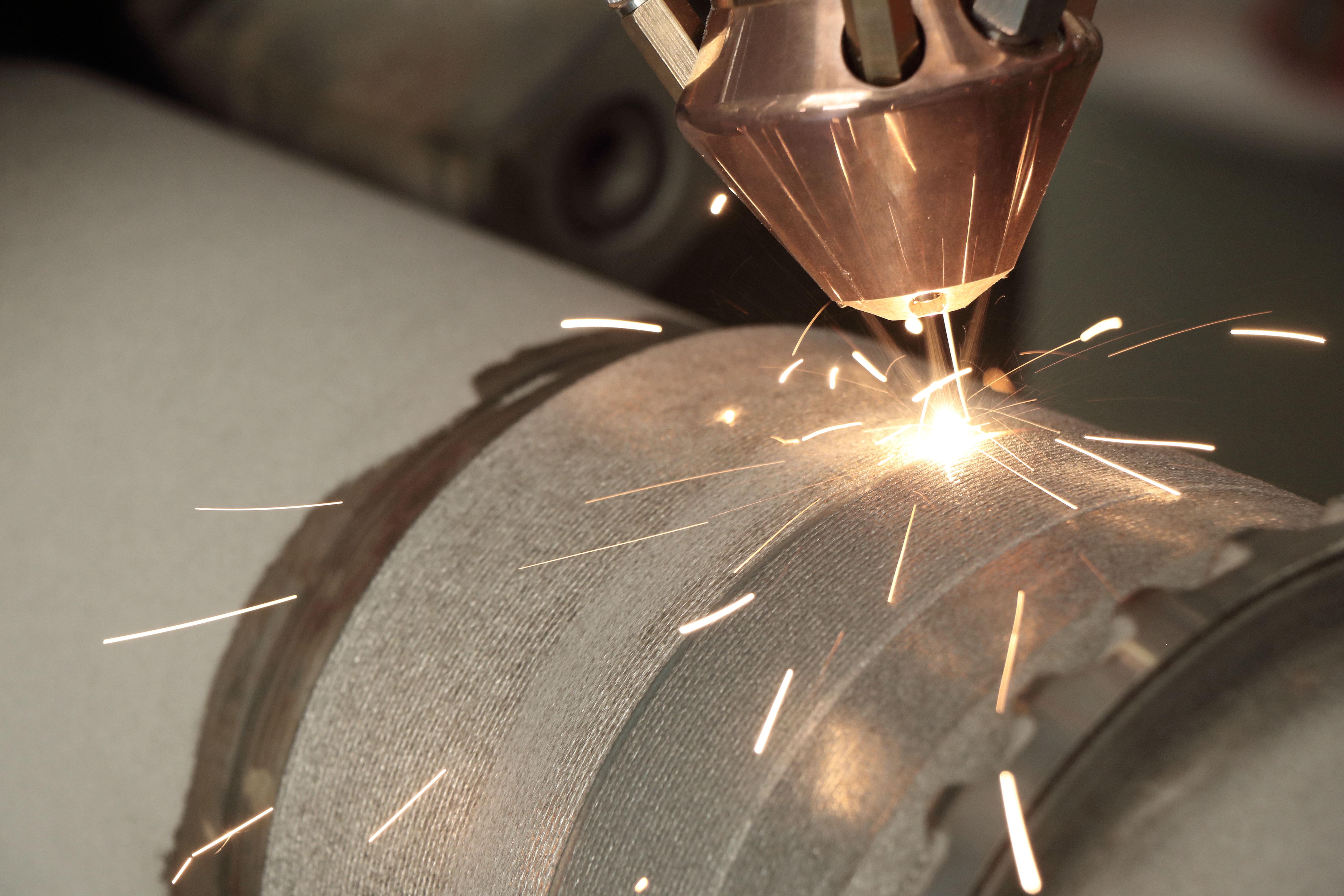
Prinzip: Verwendung eines Laserstrahls mit hoher Energiedichte zum Schmelzen von Metall zum Schweißen, schmale Schweißnaht, kleine Wärmeeinflusszone.
Vorteile:
Hohe Präzision, geeignet zum Schweißen winziger Teile.
Kleine Wärmeeinflusszone, geringe Verformung.
Nachteile:
Teure Ausrüstung, hohe Wartungskosten.
Erfordert hochpräzise Montage, kleiner Schweißspalt.
Anwendungen:Elektronik, Automobil, medizinische Geräte, optische Ausrüstung.
2.7 EBW - Elektronenstrahlschweißen
Prinzip:Schmilzt das Schweißmaterial mithilfe eines hochenergetischen Elektronenstrahls in einer Vakuumumgebung.
Vorteile:
Es können hochschmelzende Werkstoffe (Titan, Wolfram, Zirkonium) geschweißt werden.
Große Schweißtiefe, geeignet zum Schweißen dicker Platten.
Nachteile:
Muss in einer Vakuumumgebung durchgeführt werden, teure Ausrüstung.
Anwendungen: Luft- und Raumfahrt, Kernenergie, Herstellung von Präzisionsinstrumenten.
2.8 FW - Reibschweißen
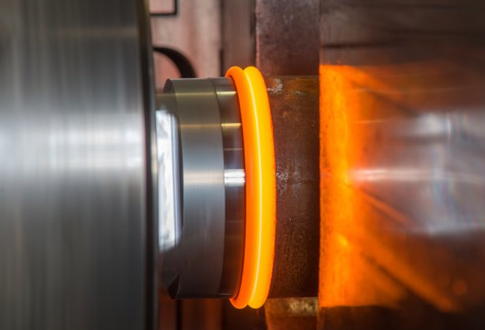
Prinzip:Beim Reibschweißen werden zwei Werkstücke mit hoher Geschwindigkeit rotiert und miteinander in Kontakt gebracht, um Reibungswärme zu erzeugen, die Kontaktflächen aufzuweichen und Druck auszuüben, um eine starke Verbindung herzustellen.
Eigenschaften
Kein Schmelzen, Festkörperschweißen, wodurch die Defekte des Schmelzschweißens (wie Porosität, Risse) vermieden werden.
Geeignet zum Schweißen unterschiedlicher Metalle, wie Aluminium-Kupfer, Edelstahl-Kohlenstoffstahl usw.
Schnelle Schweißgeschwindigkeit, normalerweise in wenigen Sekunden.
Vorteile
Hohe Schweißqualität, kein Zusatzwerkstoff erforderlich
Geeignet für die automatisierte Produktion mit hoher Wiederholgenauigkeit.
Geringer Schweißverzug, hervorragende mechanische Eigenschaften.
Nachteile
Geeignet für runde oder regelmäßig geformte Werkstücke, wie beispielsweise Wellenteile.
Höhere Gerätekosten.
Anwendungen
Antriebswellen für Autos, Bohrwerkzeuge, Teile für Raumfahrzeuge usw.
Schienenverkehr, Herstellung von Flugmotoren.
Veröffentlichungszeit: 14. März 2025