1.1 Die Wirkung des Stroms auf die Formgebung desMantelschicht
Aktuell(A) | DEpth (der Fusion)(mm) | FBodenhöhe(mm) | Breite(mm) |
70 | 0,19 | 4.26 | 16.41 |
80 | 0,35 | 4.07 | 17.08 |
90 | 0,88 | 3.43 | 17.48 |
100 | 1,03 | 2,73 | 17,58 |
110 | 1,25 | 2,65 | 18.14 |
Tabelle 3.1 Geometrie des Querschnitts der Mantelschicht bei unterschiedlichen Strömen
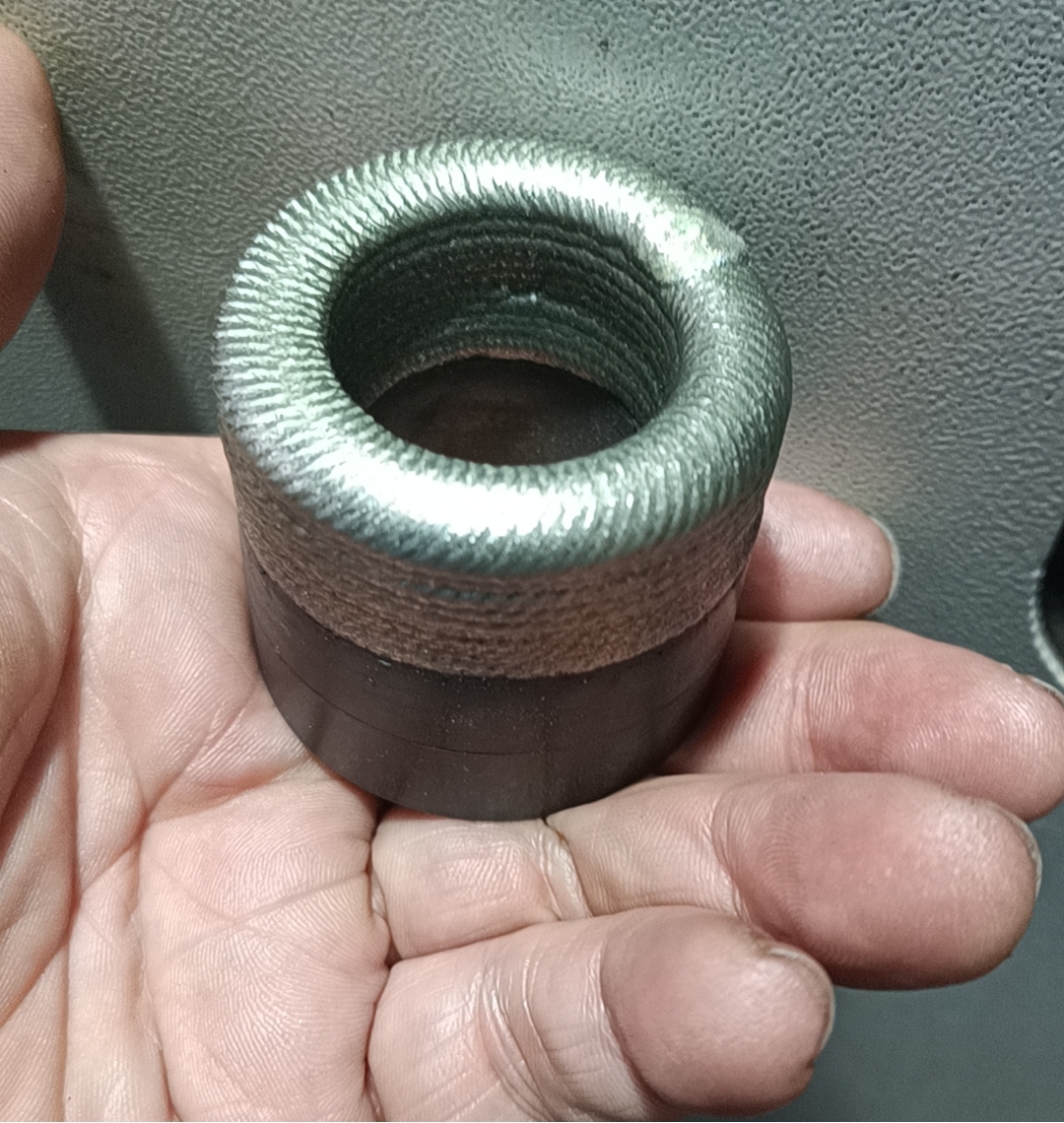
Mit zunehmender Stromstärke nehmen Tiefe und Breite der Mantelschicht zu, die Schichthöhe ab. Dies liegt daran, dass die mit zunehmender Stromstärke erzeugte Wärme nicht nur das Mantelmetall schmilzt, sondern auch einen Teil des Substrats schmilzt. Es kommt zu einer Vermischung von Mantel und Substrat, wodurch die Mantelschicht insgesamt absinkt, die Schmelztiefe zunimmt und die Schichthöhe abnimmt. Mit zunehmender Stromstärke wird der Plasmabogen gröber, der Temperaturbereich der Wärmequelle vergrößert sich, das Schmelzbad im Substrat breitet sich stärker aus und die Breite des Schmelzbads nimmt zu.
1.2 Die Wirkung vonSchweißenGeschwindigkeit beim Formen der geschmolzenen Mantelschicht
Schweißgeschwindigkeit(mm/s) | DEpth (der Fusion)(mm) | FBodenhöhe(mm) | Breite(mm) |
4 | 1.17 | 4.34 | 17,61 |
5 | 1,06 | 2,73 | 17,58 |
6 | 0,35 | 2,61 | 16,96 |
7 | 0,13 | 2,55 | 15.01 |
8 | — | — | — |
Tabelle 3.2 Querschnittsgeometrie geschmolzener Plattierungsschichten bei unterschiedlichen Schweißgeschwindigkeiten
Mit zunehmender Schweißgeschwindigkeit verringert sich die Schmelztiefe der Plattierungsschicht. Die Schichthöhe nimmt zunächst stark ab und wird dann langsam kleiner, während die Breite abnimmt. Bei einer Schweißgeschwindigkeit von 4 mm/s und einer gewissen Zunahme des Plattierungsmetalls beträgt die Schmelztiefe 1,17 mm. Zu diesem Zeitpunkt kann die Wärmezufuhr pro Längeneinheit das Grundmaterial nicht weiter zum Schmelzen bringen und die Schmelzplattierungsschicht wächst weiter auf eine Schichthöhe von 4,34 mm an. Bei einer Erhöhung der Schweißgeschwindigkeit auf 5 mm/s verringern sich die Wärmezufuhr pro Längeneinheit und die Drahtzufuhrmenge, wodurch sich Schmelztiefe, Schichthöhe und Breite verringern. Bei weiter zunehmender Schweißgeschwindigkeit reicht die Wärmezufuhr, wie oben erwähnt, zu diesem Zeitpunkt nicht aus und nur ein kleiner Teil des Grundmaterials kann schmelzen. Die Höhe der Schmelzplattierungsschicht nimmt zunächst stark ab und wird dann langsam kleiner, während die Breite abnimmt. Bei einer weiteren Erhöhung der Schweißgeschwindigkeit reicht, wie oben erwähnt, die Wärmezufuhr zu diesem Zeitpunkt nicht aus, es kann nur ein kleiner Teil des Grundwerkstoffs aufgeschmolzen werden, die Schmelzplattierungsschicht scheint nicht durchzuhängen, was zu einer stärkeren Reduzierung der Schmelztiefe führt, während die Schichthöhe weniger stark reduziert wird.
1.3 Einfluss der Drahtvorschubgeschwindigkeit auf die Formgebung der Mantelschicht
Drahtvorschubgeschwindigkeit(mm/s) | DEpth (der Fusion)(mm) | FBodenhöhe(mm) | Breite(mm) |
40 | 1,43 | 2.24 | 19,91 |
50 | 1,25 | 2,56 | 18,86 |
60 | 1,03 | 2,73 | 17,58 |
70 | 0,71 | 3,46 | 15,82 |
80 | 0,16 | 5.16 | 14.20 |
Tabelle 3.3 Geometrische Abmessungen des Querschnitts der Mantelschicht bei unterschiedlichen Drahtvorschubgeschwindigkeiten.
Mit zunehmender Drahtvorschubgeschwindigkeit nehmen Tiefe und Breite der Plattierungsschicht ab und die Schichthöhe nimmt zu. Dies liegt daran, dass bei bestimmten Stromstärken und Schweißgeschwindigkeiten auch die Wärmezufuhr pro Längeneinheit gleich ist. Mit zunehmender Drahtvorschubgeschwindigkeit steigt die Menge des Fülldrahts pro Längeneinheit und das Plattierungsmetall muss mehr Wärme aufnehmen. Wenn die Wärmezufuhr nicht ausreicht, um die gesamte Plattierungsschicht vollständig zu schmelzen, schmilzt der Teil des Grundmaterials weniger stark, sodass die Schmelztiefe abnimmt und die Schichthöhe zunimmt. Die Ausbreitungsfähigkeit des Plattierungsmetalls in der Nähe des Teils des Grundmaterials verschlechtert sich, sodass die Breite schnell abnimmt. Die Breite nimmt schnell ab.
Zusammenfassend kann man sagen, dass die effektiven Prozessparameter für das Plasma-Lichtbogen-Plattieren einer Schicht aus Duplex-Edelstahl 2205 im Bereich von 90 bis 110 A, von der Schweißgeschwindigkeit von 4 bis 6 mm/s, von der Drahtvorschubgeschwindigkeit von 50 bis 70 mm/s und von der Ionengas-Durchflussrate von 1,5 l/min liegen.
2 Basierend auf der Response-Surface-Methode zur Optimierung der Prozessparameter zur Bildung der Schmelzplattierungsschicht
Die Response-Surface-Methode (RSM) ist eine Kombination aus experimentellem Design und statistischen Optimierungstechniken. Durch die Analyse von Testdaten können Einflussfaktoren und Antwortwerte aus der Anpassungsfunktion und der dreidimensionalen Oberflächenkarte abgeleitet werden. Die Beziehung zwischen Einflussfaktoren und Antwortwerten im tatsächlichen Test kann intuitiv wiedergegeben werden und hat eine prädiktive und optimierende Funktion. Aus den oben genannten Gründen wird RSM im Central Composite Design (CCD) ausgewählt, um ein Prozessoptimierungsprogramm zu entwickeln. Dabei werden die Beziehungen zwischen Stromstärke, Schweißgeschwindigkeit, Drahtvorschubgeschwindigkeit, Verdünnungsrate und Seitenverhältnis der Schmelzplattierungsschicht untersucht und durch mathematische Modellierung die Qualität der Schmelzplattierungsschicht aus den Prozessparametern, der Verdünnungsrate und dem Seitenverhältnis der Funktion abgeleitet.
2.1 Der Einfluss der Prozessparameter auf die Verdünnungsrate der Mantelschicht.
Tabelle 3.8 Ergebnisse und Verifizierung der Prozessoptimierung
Gruppe | X1(A) | X2(mm·s-1) | X3(mm·s-1) | Verdünnungsverhältnis(%) | Seitenverhältnis |
Vorhersagegruppe | 99 | 6 | 50 | 14.8 | 4.36 |
Testgruppe 1 | 99 | 6 | 50 | 13.9 | 4.13 |
Testgruppe 2 | 99 | 6 | 50 | 15,5 | 4,56 |
Testgruppe 3 | 99 | 6 | 50 | 14.3 | 4.27 |
Durchschnittlicher Fehler | 2.9 | 2.3 |
(PTA-Schweißen von Shanghai Duomu)
Abbildung 3.16 Testergebnisse für optimale Prozessparameter (a) Testgruppe 1; (b) Testgruppe 2; (c) Testgruppe 3
Hochwertige Plattierungsschichten zeichnen sich durch eine geringe Verdünnungsrate und ein großes Aspektverhältnis aus. Die optimalen Prozessparameter sind: Stromstärke 99 A, Schweißgeschwindigkeit 6 mm/s, Drahtvorschubgeschwindigkeit 50 mm/s. Die durchschnittliche Verdünnungsrate der im optimalen Verfahren hergestellten Plattierungsschicht beträgt etwa 14,6 %, das durchschnittliche Aspektverhältnis 4,33. Der durchschnittliche Fehler zwischen Modellvorhersagewert und experimentellem Wert liegt unter 5 %, was auf eine hohe Modellgenauigkeit und eine gute Qualität der im optimalen Verfahren hergestellten Plattierungsschicht hindeutet.
Veröffentlichungszeit: 31. Januar 2024