Automatisierte Laserauftragsschweiß- und Schweißgeräteist eine Industrieanlage, die einen energiereichen Laserstrahl nutzt, um ein Beschichtungsmaterial, beispielsweise ein Legierungspulver oder einen Draht, auf die Oberfläche eines Metallsubstrats zu schmelzen und aufzutragen. Diese Technologie verbessert die Oberflächeneigenschaften des Werkstücks, wie Verschleiß-, Korrosions- und Hochtemperaturbeständigkeit, und senkt gleichzeitig die Kosten und verlängert die Lebensdauer der Komponenten. Das automatisierte System gewährleistet hohe Präzision und effizienten Betrieb und eignet sich für die Massenproduktion und Reparatur komplexer Teile.
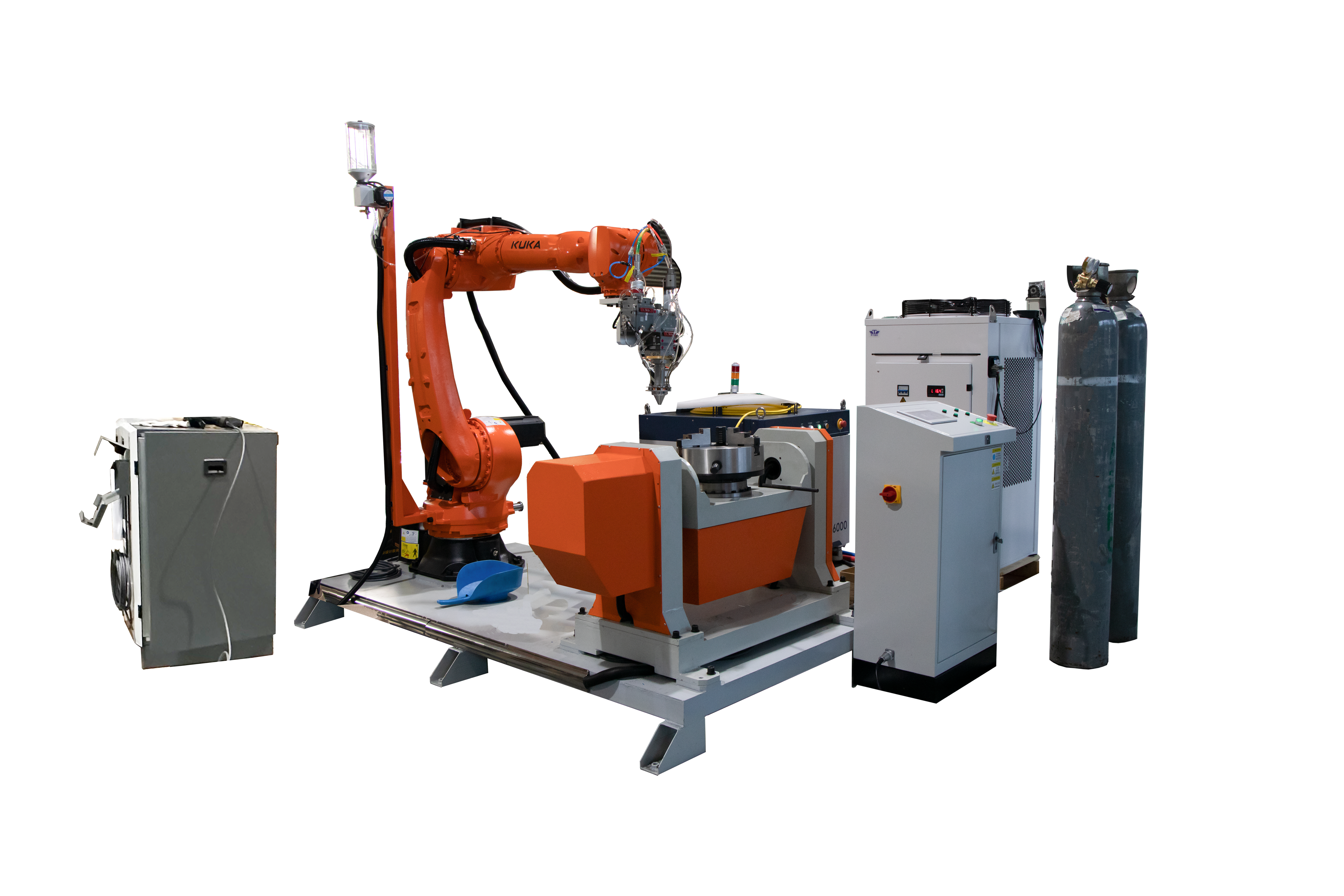
I. Funktionsprinzip
1. Fokussierung des Laserstrahls:Der hochenergetische Laserstrahl wird durch das optische System auf die Oberfläche des Werkstücks fokussiert.
2. Materialschmelzen:Das geschmolzene Material (Pulver oder Draht) wird über das Pulver- oder Drahtzufuhrsystem in das Laserschmelzbad geleitet.
3. Poolbildung:Der Laser schmilzt die Oberfläche des Substrats und bildet ein Schmelzbad, in dem das Mantelmaterial mit dem Substrat verschmilzt.
4. Schnelles Abkühlen:Die Schmelzschicht wird schnell abgekühlt und verfestigt, wodurch eine Schmelzschicht entsteht, die metallurgisch mit dem Grundmaterial verbunden ist.
II.Zusammensetzung der Ausrüstung
1. Lasersystem
- Lasertyp:Faserlaser, CO₂-Laser, Halbleiterlaser.
- Leistungsbereich: in der Regel zwischen500 WUnd10 kW, abhängig von den Prozessanforderungen.
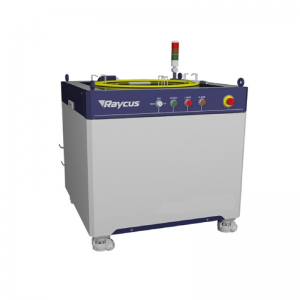
2. Pulver-/Drahtzufuhrsystem
-Pulverförderer: Präzise Steuerung der Zufuhr des Verkleidungsmaterials, um die Gleichmäßigkeit der Verkleidungsschicht sicherzustellen.
- Drahtvorschub: Geeignet für dickere Mantelschichten.
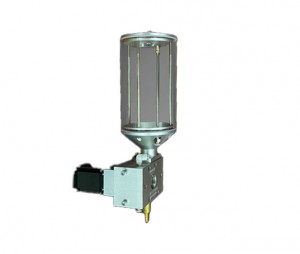
3. CNC-Bewegungssystem
- 3-Achsen-/5-Achsen-CNC-Plattform: Steuern Sie die Bewegung des Laserkopfes oder Werkstücks, um komplexe Formverkleidungen zu realisieren.
- Robotersystem: geeignet für die Mehrwinkelbearbeitung komplexer Werkstücke.
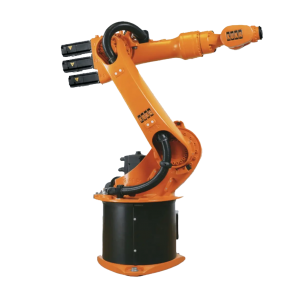
4. Kühlsysteme
- Laserkühlung: Normalerweise wird ein Wasserkühlsystem verwendet, um den Laser stabil am Laufen zu halten.
- Werkstückkühlung: um Verformungen oder Leistungseinbußen durch Überhitzung zu vermeiden.
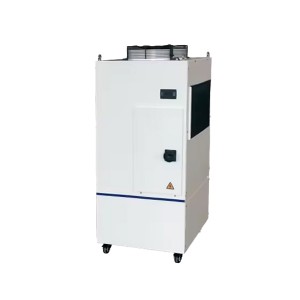
5. Automatisches Kontrollsystem
- Softwaresystem:CAD/NOCKENProgrammierung zur Unterstützung der automatisierten Produktion.
- Überwachungssystem: Echtzeitüberwachung von Temperatur, Laserleistung und Schmelzbadstatus während des Schmelzprozesses.
III. Prozessmerkmale und Vorteile
1. Hohe Präzision und Effizienz
- Die Laserstrahlsteuerung ist präzise und die Dicke der Mantelschicht kann im Bereich von0,1–5 mm.
- Das automatisierte Kontrollsystem gewährleistet die Konsistenz und Effizienz der Verarbeitung.
2. Starke Materialverträglichkeit
- Unterstützt eine Vielzahl von Verkleidungsmaterialien:auf Eisenbasis, auf Nickelbasis, KobaltbasislegierungenUndVerbundwerkstoffe.
- Es können Verbundverkleidungen zwischen verschiedenen Materialien realisiert und die Leistung verbessert werden.
3. Kleine Wärmeeinflusszone
- Laserauftragschweißen mit lokaler Erwärmung, geringe Verformung des Substrats, geeignet für die Bearbeitung von Präzisionsteilen.
4. Metallurgische Bindung
- Metallurgische Bindung zwischen der Plattierungsschicht und dem Grundmaterial, hohe Bindungsstärke, wodurch Delaminations- oder Ablöseprobleme vermieden werden.
5. Reparatur und Stärkung
- Geeignet zur Reparatur abgenutzter oder beschädigter hochwertiger Teile wie Formen, Lager, Motorteile usw.
IV. Anwendungsbereiche
•Formenbau und Reparatur
•Luft- und Raumfahrt
•Automobilindustrie
•Petrochemische Industrie
•Schwere Maschinen
V. Wichtige Punkte zur Geräteauswahl
1. Anforderungen an die Laserleistung
- Dünnschichtverkleidung:500 W bis 2 kW
- Dickschichtschweißen:3 kW bis 10 kW
2. Verarbeitungspräzision
- Wenn hohe Präzision erforderlich ist, wählen Sie ein Gerät mit geschlossenem Regelkreis.
3. Schmelzmaterialtyp
- Wählen Sie je nach Material des Werkstücks und der Verwendungsumgebung das geeignete Pulverzufuhr- oder Drahtzufuhrsystem.
4. Arbeitsraum und Flexibilität
- Stellen Sie sicher, dass der Bewegungsbereich des Gerätetisches oder Roboterarms den Produktionsanforderungen entspricht.
VI.der zukünftige Entwicklungstrend
1. Intelligente Steuerung
- Integration von künstlicher Intelligenz und maschinellem Lernen zur Optimierung der Parameter des Beschichtungsprozesses und Verbesserung der Verarbeitungsqualität.
2. Verbundverkleidungstechnologie
- Entwicklung einer mehrschichtigen Verbundwerkstoffverkleidung, um den Anforderungen höherer Leistung gerecht zu werden.
3. Umweltschutz und Energieeinsparung
- Entwicklung eines effizienteren und energiesparenderen Laserbeschichtungssystems zur Reduzierung des Ressourcenverbrauchs.
Automatische Laserauftragsschweiß- und -auftragsschweißgeräteist ein wichtiges technisches Werkzeug in der modernen Fertigungsindustrie, das aufgrund seiner hohen Präzision, Automatisierung und Materialkompatibilität in verschiedenen High-End-Fertigungs- und Reparaturbereichen weit verbreitet ist.
Veröffentlichungszeit: 02.12.2024