مبادئ عملية ترسيب EDM
عملية ترسيب EDM هي مصدر طاقة عالي الطاقة المخزن بين القطب المعدني والمادة الأساسية مع إطلاق فوري عالي التردد، من خلال تأين الغاز بين مادة القطب والمادة الأساسية، وتشكيل عدد من قنوات القوس الدقيقة، بحيث ينتج سطح المادة الأساسية منطقة دقيقة عالية الحرارة لحظية، مادة القطب في مجال كهربائي دقيق تحت تأثير اللحام بالانصهار مع ركيزة المادة الأساسية، وتشكيل الرابطة المعدنية. عملية EDM هي منطقة دقيقة من عملية التبريد اللحظي المتكرر بدرجة حرارة عالية، وهي تختلف عن اللحام التقليدي، حيث لا ترتفع درجة حرارة المادة الصلبة بشكل أساسي، وبالتالي لن تنتج إجهادًا أو تشوهًا أو ظواهر أخرى.
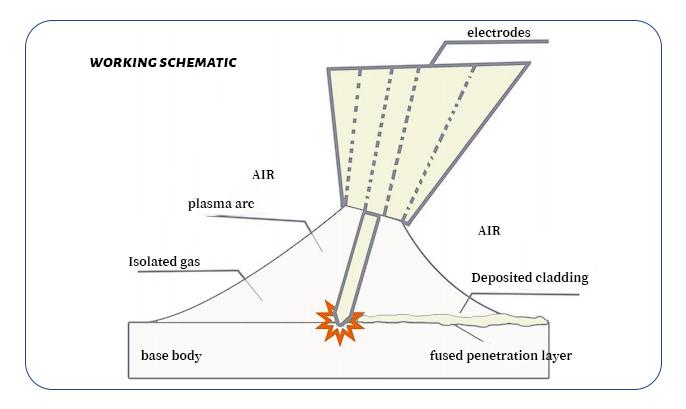
الميزات التقنية
عملية ترسيب EDM، المعروفة أيضًا باسم التكسية القوسية، هي عملية تستخدم الحرارة الناتجة عن تفريغ شرارة كهربائية لصهر وترسيب المواد المعدنية. ومن أهم مزاياها وفوائدها:
1. دقة عالية: نظرًا لأن EDM يتم تحقيقه عن طريق التحكم الدقيق في التيار والجهد، فإن عملية الكسوة دقيقة للغاية ويمكنها تحقيق التحكم الدقيق في الشكل والحجم.
2. كفاءة عالية: إن كسوة EDM سريعة نسبيًا ويمكنها إصلاح أو تحسين الأجزاء البالية أو التالفة الموضعية من قطعة العمل بسرعة، مما يزيد من الإنتاجية.
3. المرونة: هذه العملية مناسبة لمجموعة متنوعة من الأشكال المعقدة ومساحات الإصلاح الصغيرة، بغض النظر عن شكل وحجم قطعة العمل.
4. منطقة صغيرة متأثرة بالحرارة: بالمقارنة مع اللحام التقليدي، فإن منطقة التأثر بالحرارة في الكسوة EDM صغيرة، مما يكون له تأثير أقل على تشوه وإجهاد قطعة العمل ويحتفظ بالأداء الأصلي لقطعة العمل.
5. اختيار واسع من المواد: يمكن إصلاح أو تحسين جميع المواد المعدنية تقريبًا بواسطة الكسوة EDM، بما في ذلك كربيد الأسمنت والفولاذ المقاوم للصدأ وسبائك الألومنيوم وما إلى ذلك.
6. صديق للبيئة: بالمقارنة مع اللحام بالاندماج، فإن كسوة EDM تنبعث منها أبخرة وغازات ضارة أقل ولها تأثير أقل على البيئة.
7. الإصلاح عبر الإنترنت: دون توقف الإنتاج، يمكن إجراء الإصلاح على المعدات قيد التشغيل، وهو أمر مفيد للغاية لصيانة بعض المعدات الحيوية.
بشكل عام، تعتبر عملية ترسيب EDM وسيلة سريعة ودقيقة ومرنة وصديقة للبيئة للإصلاح والتقوية.
إصلاح عيوب سطح غلاف الحديد الزهر
عملية ترسيب أسطح EDM مقابل اللحام الرقعي التقليدي
تعد عملية ترسيب EDM (لحام القوس البلازمي) ولحام الحشو التقليدي (لحام MIG) من تقنيات اللحام المستخدمة بشكل شائع، ولكن لديهما بعض الاختلافات من حيث المبدأ والمزايا والعيوب ونطاق التطبيق.
١. مبدأ مختلف: تستخدم عملية ترسيب EDM شرارة كهربائية كمصدر حرارة للحام، وتُولّد شرارة كهربائية عالية الحرارة ومنخفضة الضغط من خلال مجال كهرومغناطيسي عالي التردد، مما يُحقق اندماج المواد. أما لحام الحشو التقليدي، فيعتمد على لحام تيار أكسيد الليثيوم (مسدس MIG) كمصدر حرارة، ويُنجز اللحام عن طريق حجب منطقة اللحام بغازات مثل ألكان أكسيد الليثيوم (CO2) أو ألكان أكسيد النيتروجين (الأرجون).
٢. اختلافات في الدقة: توفر عملية ترسيب التفريغ الكهربائي (EDM) دقة عالية وكثافة عالية لكبسولات اللحام، مما يجعلها مناسبة لعمليات اللحام التي تتطلب دقة وقوة عالية. على الرغم من أن اللحام بالحشو التقليدي يُحقق أداءً جيدًا في العديد من التطبيقات، إلا أن دقته وكثافة كبسولات اللحام فيه أقل قليلاً من عملية ترسيب التفريغ الكهربائي (EDM).
٣. نطاق تطبيقي متنوع: تُطبق عملية ترسيب EDM على مجموعة متنوعة من المواد المعدنية، بما في ذلك الفولاذ والألمنيوم والنيكل والرصاص، ولها تطبيقات واسعة. يُستخدم لحام الإصلاح التقليدي بشكل رئيسي على الألياف المطاطية والسبائك والألمنيوم وغيرها من المواد، ونطاق تطبيقه ضيق نسبيًا.
٤. أداء بيئي متميز: لا تُنتج عملية ترسيب EDM نفايات خطرة، وتتميز بأداء بيئي أفضل. في اللحام بالحشو التقليدي، قد يُنتج أكسيد الليثيوم (CO2) كغاز عازل نفايات خطرة، مما يؤثر سلبًا على البيئة.
٥. اختلافات في صعوبة التشغيل: عملية ترسيب EDM سهلة التشغيل نسبيًا وتتميز بسهولة المناورة. بينما يُعدّ لحام الحشو التقليدي أكثر تعقيدًا من حيث صعوبة التشغيل ويتطلب مهارات وخبرة أكبر.
باختصار، هناك بعض الاختلافات بين عملية ترسيب EDM ولحام الحشو التقليدي من حيث المبدأ، والدقة، ونطاق التطبيق، والأداء البيئي، وصعوبة التشغيل. وفقًا لاحتياجات التطبيق المحددة ونوع المادة، يمكن اختيار تقنية اللحام الأنسب.
روابط المنتجات ذات الصلة
https://www.ourcladding.com/intelligent-edm-cladding-repair-machine-esd-9100-product/
https://www.youtube.com/watch?v=8vFi1XloPQI
وقت النشر: ٨ أبريل ٢٠٢٤