إن استخدام تقنية الكسوة البلازمية لتقوية سطح رؤوس الحفر PDC هي وسيلة فعالة لتحسين مقاومتها للتآكل ومقاومة التأثير ومقاومة التآكل.
1. مرحلة التحضير
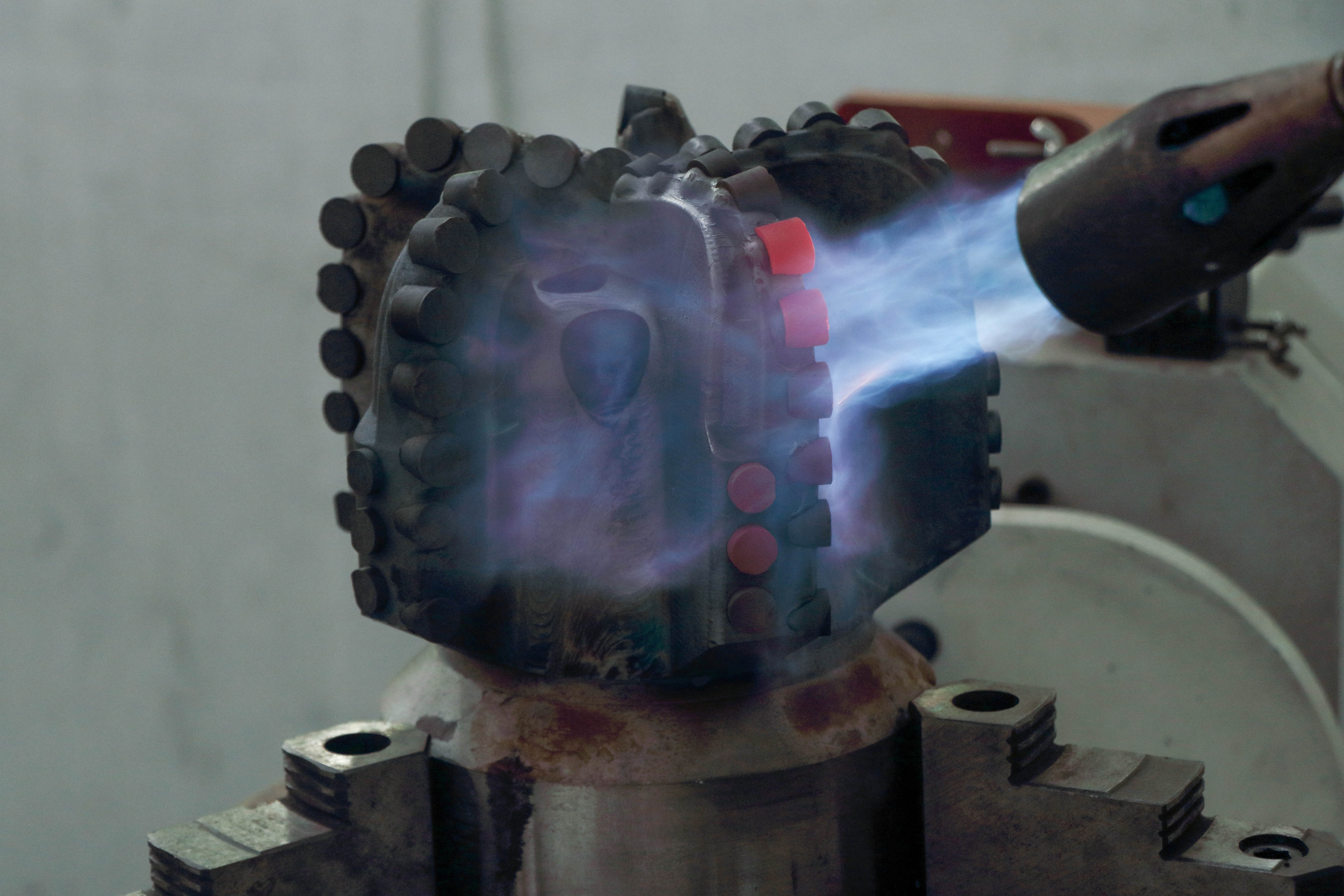
(1) تحديد مادة الكسوة
- مواد الكسوة المستخدمة بشكل شائع:
- سبيكة أساسها الكوبالت: مقاومة عالية للتآكل والتآكل.
- سبيكة أساسها النيكل: مقاومة للأكسدة ذات درجات الحرارة العالية والتآكل الكيميائي.
- السبائك القائمة على الحديد: فعالة من حيث التكلفة ومناسبة لمتطلبات مقاومة التآكل المتوسطة.
- سبائك معززة بجسيمات السيراميك: على سبيل المثال WC (كربيد التنغستن)، TiC (كربيد التيتانيوم)، وما إلى ذلك لمتطلبات مقاومة التآكل العالية جدًا.
(2) تحديد مساحة الكسوة
- يستهدف الغلاف المندمج لرؤوس الحفر PDC عادةً ما يلي:
- جزء الجانب: لتعزيز مقاومة التآكل وتقليل الاحتكاك وفقدان القطع.
- سطح الهيكل: لتعزيز مقاومة التآكل والصدمات بشكل عام.
(3) المعالجة المسبقة للسطح
- تنظيف منطقة الكسوة لإزالة الزيوت والأكاسيد والطلاءات والشوائب.
- المعالجة الميكانيكية بالطحن أو النفخ الرملي لزيادة خشونة السطح وتحسين التصاق طبقة الكسوة المندمجة مع الركيزة.
2. تنفيذ عملية الكسوة
(1) إعداد معدات الكسوة البلازمية
- تكوين المعدات:
مسدس لحام البلازما, وحدة تغذية المسحوق, آلة لحام البلازما الآلية، إلخ..
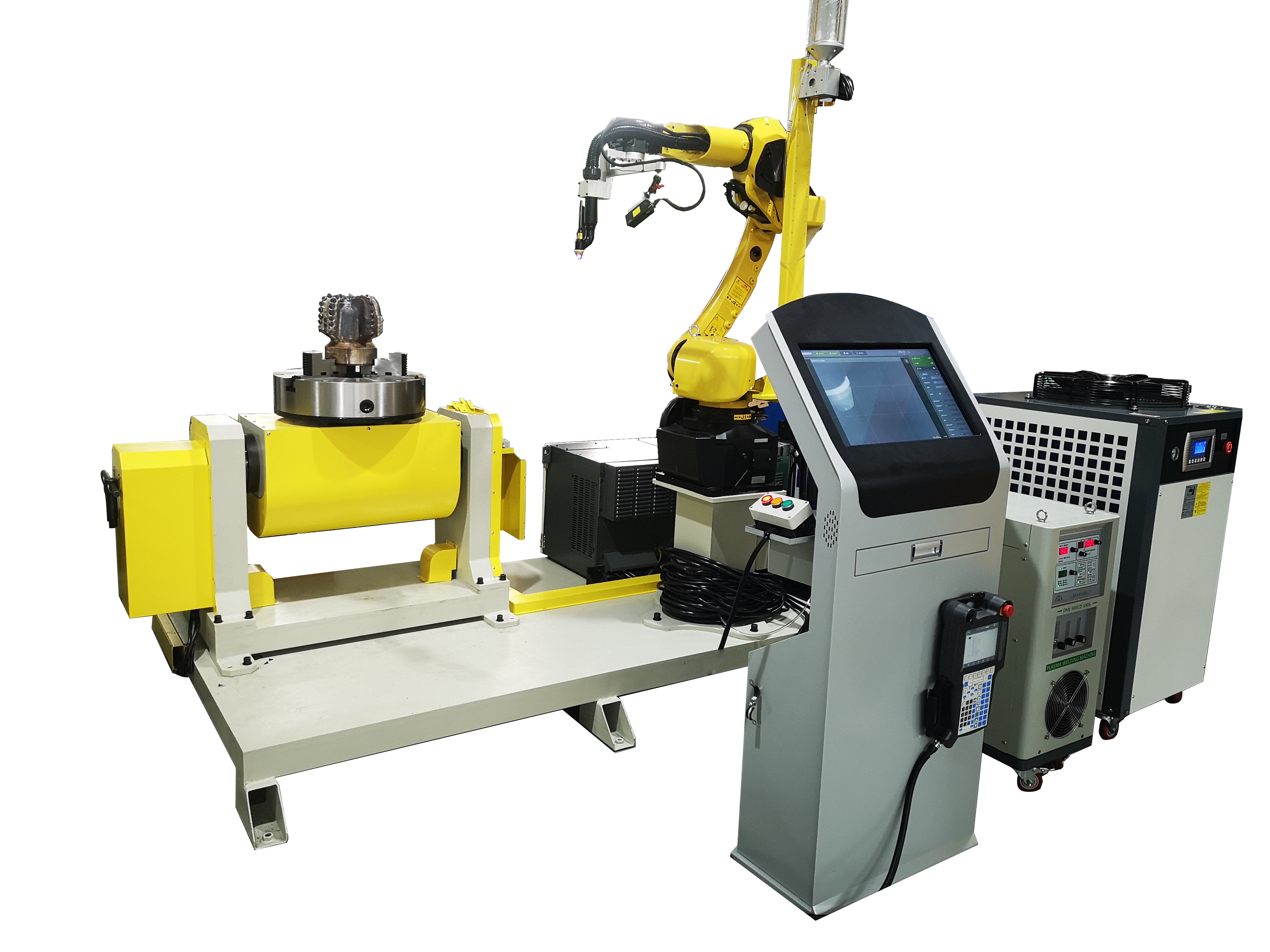
- ضبط المعلمات الرئيسية:
- التيار القوسي والجهد: يتم اختيارهما وفقًا للمادة المراد طلائها، وعادةً ما يكونان في نطاق 100-300 أمبير.
- مدخلات الحرارة: يتم تعديلها للتحكم في تشوه الركيزة ومعدل التخفيف.
- معدل تغذية المسحوق: عادة في نطاق 10~50 جرام/دقيقة لضمان توحيد طبقة الكسوة.
(2) تنفيذ الكسوة
- عملية الكسوة:
1. بدء قوس البلازما، وتشكيل بركة ذوبان عالية الحرارة.
2. من خلال نظام تغذية المسحوق، يتم رش مادة المسحوق في حوض المنصهر وربطها معدنيًا بالركيزة.
3. وفقًا لشكل مِثقب الحفر، على طول المسار المحدد للكسوة الموحدة، لضمان عدم وجود تسرب للكسوة أو الذوبان الزائد.
- التحكم في التأثير الحراري: تجنب ارتفاع درجة الحرارة أو تشوه ركيزة مثقاب PDC عن طريق ضبط معلمات قوس البلازما وطريقة التبريد.
(3) معالجة التبريد
- التبريد الطبيعي أو اعتماد طريقة التبريد بالسرعة المتحكم بها لتجنب الشقوق الناتجة عن الإجهاد الحراري.
3. مرحلة ما بعد العلاج
(1) فحص جودة الكسوة
- فحص المظهر: لاحظ ما إذا كانت طبقة الكسوة موحدة وخالية من الشقوق والثقوب الهوائية.
- اختبار الأداء: قياس الصلابة، والسمك (عادة في 0.5 ~ 3 مم)، وقوة الترابط وغيرها من المؤشرات.
- الاختبار غير المدمر: استخدم الاختبار بالموجات فوق الصوتية أو الأشعة السينية لاستكشاف الأخطاء وإصلاحها.
(2) التشطيب
- إذا كان السطح خشنًا بعد الكسوة الانصهارية، فإن المعالجة بالتحويل أو الطحن مطلوبة لتلبية متطلبات الحجم والشكل لبتات الحفر PDC.
(3) تحسين الأداء
- المعالجة الحرارية: إخماد أو تهدئة طبقة الكسوة المندمجة إذا لزم الأمر لتحسين خصائصها التنظيمية بشكل أكبر.
4. الاحتياطات
1. تجنب الضرر الناتج عن ارتفاع درجة الحرارة
- أثناء عملية تغليف البلازما، يجب التحكم بدقة في مدخلات الحرارة لتجنب التلف الحراري لإدخال PDC والركيزة.
2. مطابقة المواد
- يجب أن تتطابق مادة الكسوة مع مادة ركيزة بت PDC لضمان قوة الترابط واتساق الأداء.
3. الرقابة البيئية
- قدر الإمكان في بيئة ذات رطوبة منخفضة أو غازات واقية لتجنب الأكسدة التي تؤثر على جودة الكسوة.
يمكن استخدام هذه العملية لتحسين أداء بتات PDC الجديدة وكذلك لإصلاح البتات البالية.
وقت النشر: 9 يناير 2025